Having researched, bought and trained to work with the various technically sound equipments for carrying out quality tests, we have managed to assure delivery of top-end products to the clients. Some of the machines at our plant that carry out quality checks are:
4140 / EN19 / 42CrMo4 Bars – Test Process Chart
Test Name | Purpose | Standard/Method | Stage |
---|---|---|---|
Chemical Composition Analysis | Verifies material grade and alloy content | ASTM E415 / Optical Emission | Raw Material |
Ultrasonic Testing (UT) | Detects internal flaws or voids | ASTM A388 | After Forging/Rolling |
Hardness Testing | Measures surface hardness | ASTM E18 (Rockwell) / Brinell | Final Product |
Tensile Test | Determines tensile strength, yield, and elongation | ASTM A370 | After Heat Treatment |
Impact Test (Charpy V-Notch) | Measures toughness at room or sub-zero temperatures | ASTM E23 | On Request / Critical Apps |
Microstructure Examination | Evaluates grain structure, inclusion, and phase distribution | ASTM E112 | After Heat Treatment |
Magnetic Particle Inspection (MPI) | Detects surface and near-surface cracks in ferromagnetic materials | ASTM E709 | Post Machining |
Dimensional Inspection | Verifies size, tolerance, and straightness | As per client specs | Final QC |
Surface Finish Inspection | Checks for scale, rust, cracks, and finish quality | Visual / Manual | Final QC |
Heat Treatment Report | Confirms process parameters: temperature, duration, cooling medium | Internal Record / Cert | Post HT |
Third-Party Inspection (Optional) | Ensures compliance by external certifying agencies like BV, SGS, TUV, etc. | Client-Specified | Final Dispatch |
.jpg)
Ultrasonic Testing (UT)
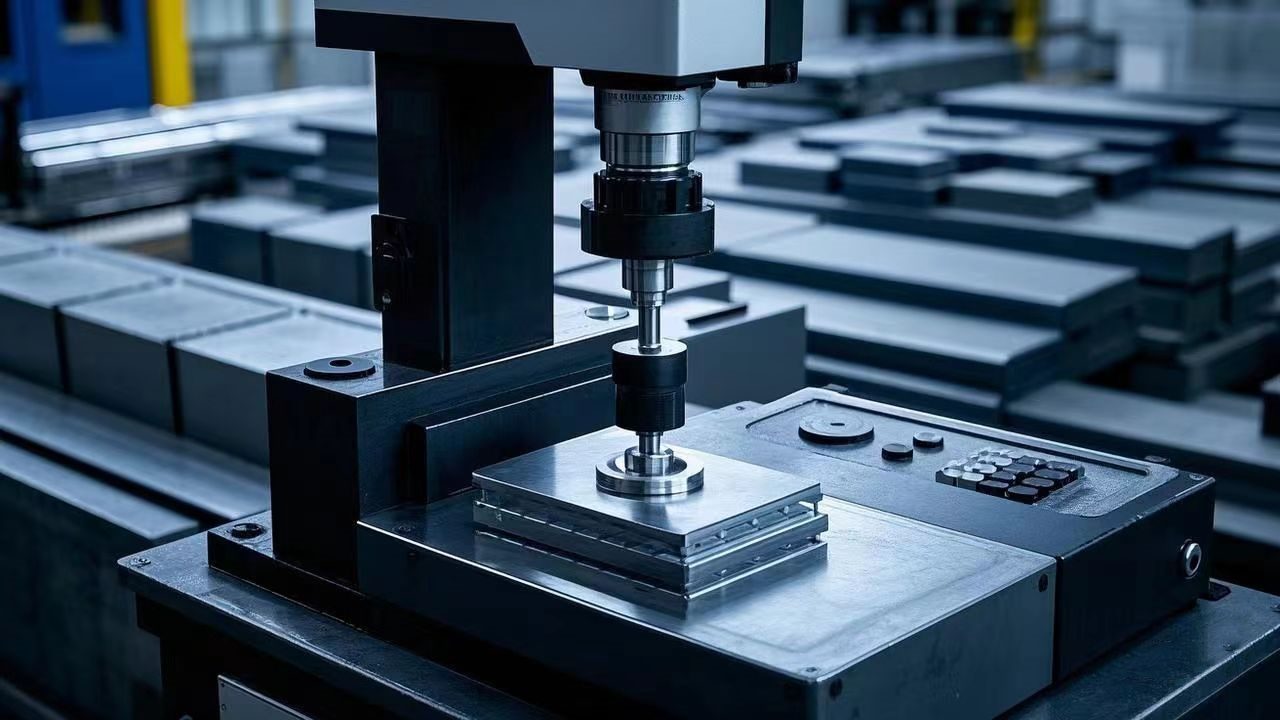
Hardness Testing
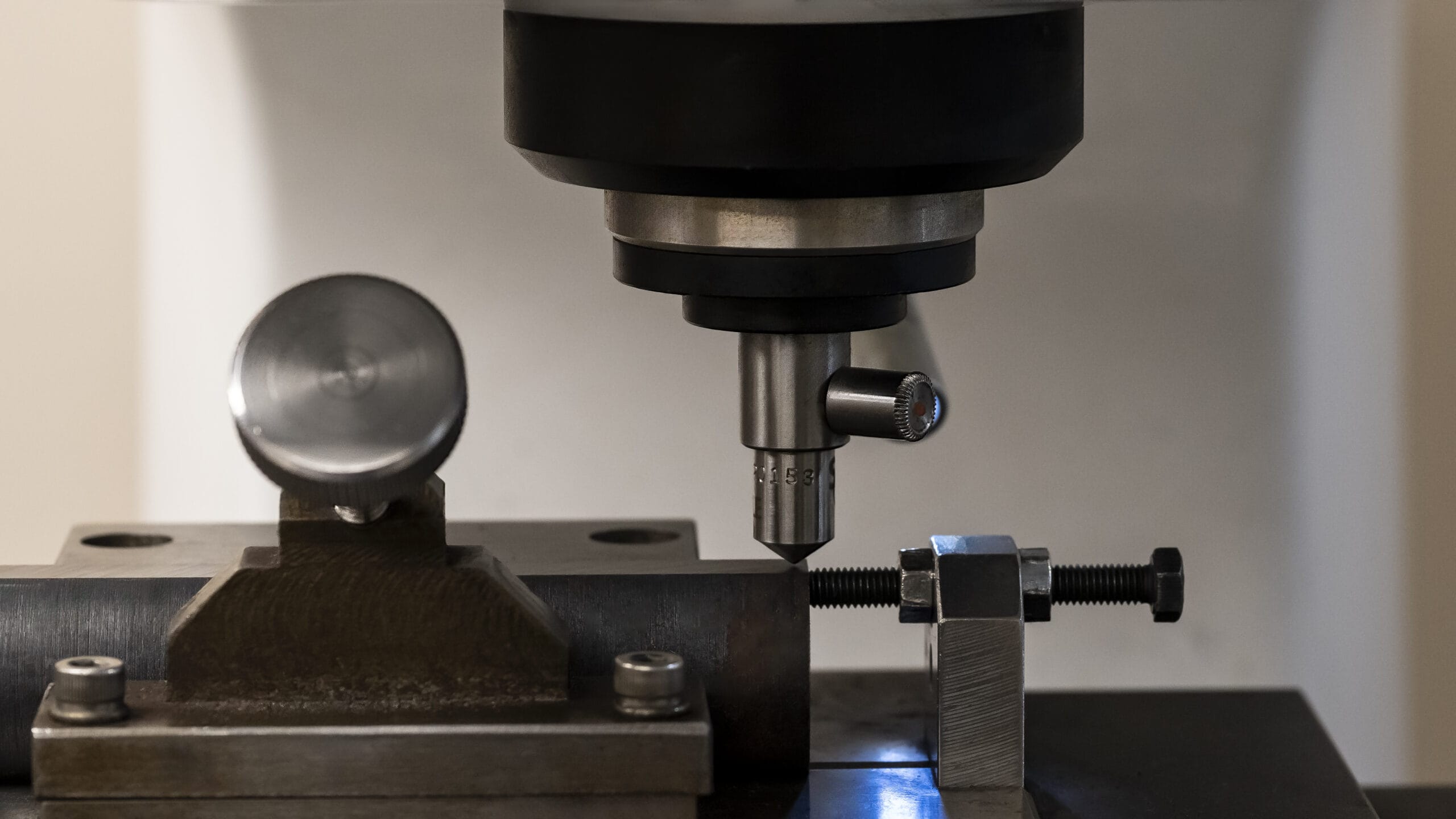
Surface Finish Inspection
.png)
Impact Test (Charpy V-Notch)
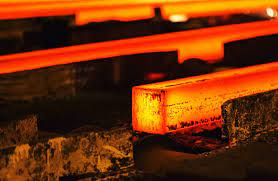
Heat Treatment Report
.jpg)
Magnetic Particle Inspection (MPI)
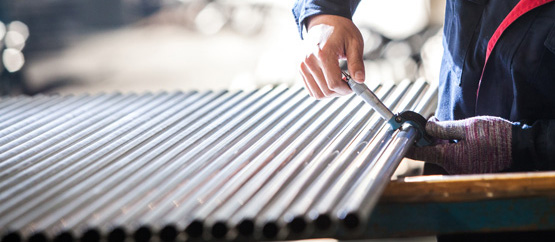
Dimensional Inspection
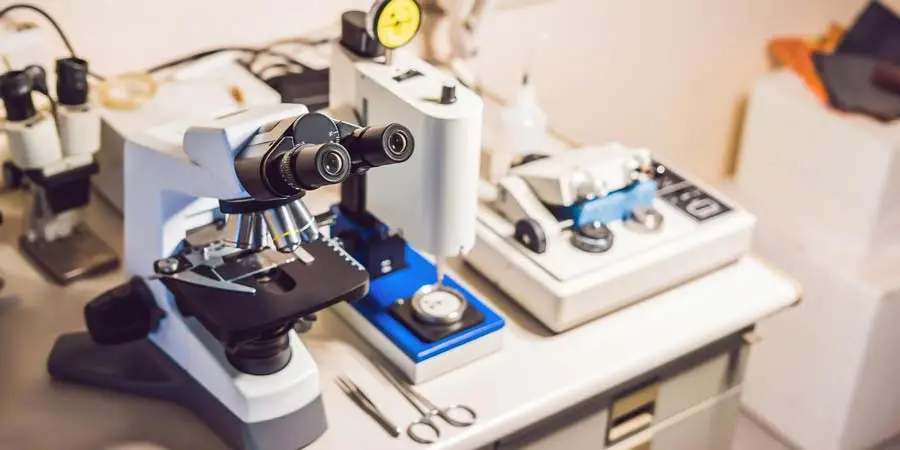
Microstructure Examination
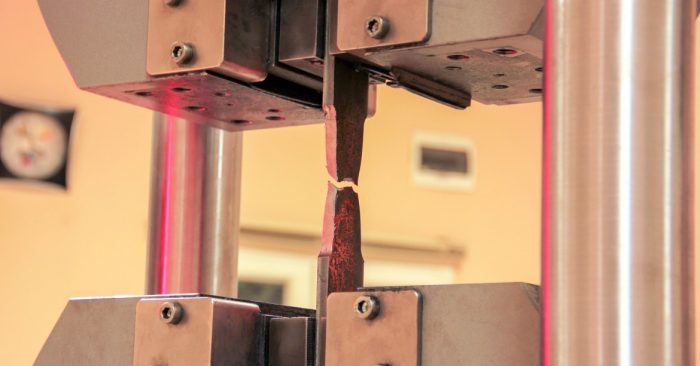
Tensile Test